Annealing
The Basics
When any material is heated, it expands; when cooled, it will contract. Since most plastics are poor conductors of heat, any uneven or rapid heating and cooling can introduce "stress" into the material. Examples of these stress-inducing processes include molding, casting, extrusion, heat- or cold-forming, cutting, drilling and machining.
Machined stress is often created when drilling deep holes, machining inside corners without proper radius (threaded holes), removing large amounts of material at high speeds, or when material is removed unevenly when reducing finished part thickness, such as in a hollow cup- or box-shaped part. Stress may also be caused by using improper (oil-based) or insufficient coolant.
Stress Problems
Stress in a plastic material or part can result in poor performance in an application , including warping, twisting, or other dimensional changes. It may also cause cracking or "crazing" (a large network of tiny cracks), poor chemical resistance, and reduced wear resistance. In addition, some plastics are more susceptible to stress than others, especially when temperature cycling (sterilization) or chemicals are used.
Contact us to determine if your material selection or part design may cause or increase stress in your finished machined parts. Frequently, subjecting the parts to a properly specified annealing cycle can reduce or eliminate "stress" in the material which has been caused by the molding, forming, or machining process.
The Solution
Annealing for plastic materials or parts is the process of heating and cooling them slowly to relieve the stress and prevent it from recurring. The cycle of temperature and time is different for each type of plastic and part cross-section. Generally, the annealing process includes heating a plastic to a temperature just below its softening point, keeping it at the high temperature for a period of time, then cooling it very slowly until it returns to room temperature.
Boedeker Plastics has several temperature-controlled ovens that are used to anneal plastic materials (sheet, rod and tube) and machined parts. The annealing may be performed before, during and after machining to reduce or eliminate stress.
Our Annealing Ovens
- Grieve AA-650 Universal Heat Treat Oven
- Grieve AB-650 Universal Heat Treat Oven
- Grieve AG-650 Universal Heat Treat Oven
Contact us to determine oven availability or to discuss your application. Our full CNC machine shop is also an available option for those customers without machining capacity, or who may have experienced difficulty with stress in plastic machined parts.
Centerless Grinding
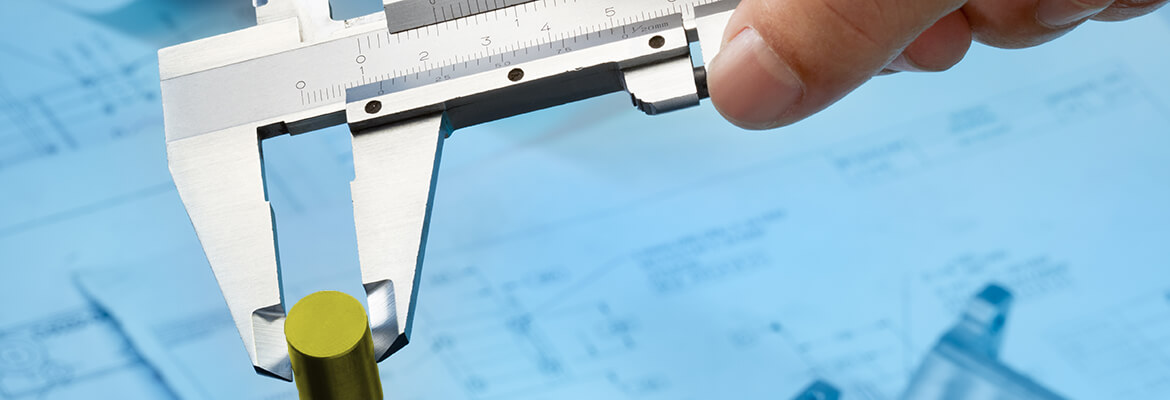
We utilize multiple centerless grinding machines to offer our clients precise diameters with improved roundness. This process has three components including a grinding wheel, regulating wheel and workblade. The work piece is rotated and held between the wheels with a specific speed and rate to achieve the desired diameter.
Centerless grinding offers improved roundness, surface finish and tolerances. This process gives our clients a cost-effective solution for tighter tolerance diameters and custom diameters that can help eliminate additional machining time during their machining process.
Contact us to see if your application is a fit for centerless grinding.
Cryogenic Deburr Technology
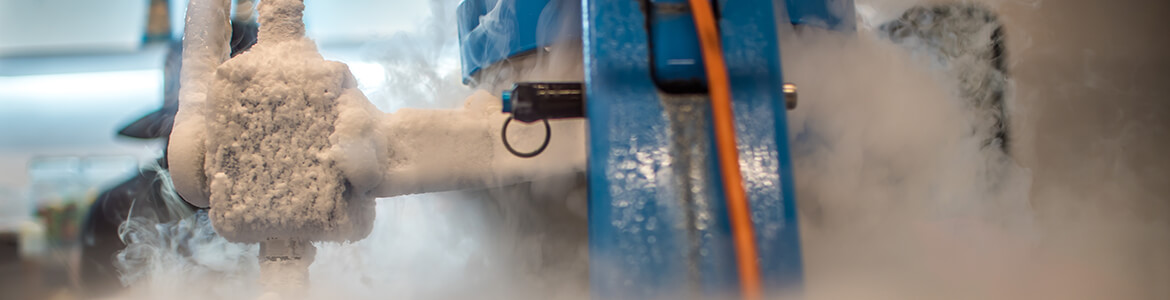
We utilize cryogenic deburring technology as a secondary finishing process. This process removes burrs and other defects at cryogenic temperatures utilizing a non-abrasive process, the low temperature causes the burrs or defects to become brittle and break away cleanly from the part.
Depending on part size and material type this process can be used to process a large quantity of parts per cycle for critical tolerance parts, offering a cost effective deburring solution.
Contact us to evaluate your parts for cryogenic deburring.

Laser Marking & Part Engraving
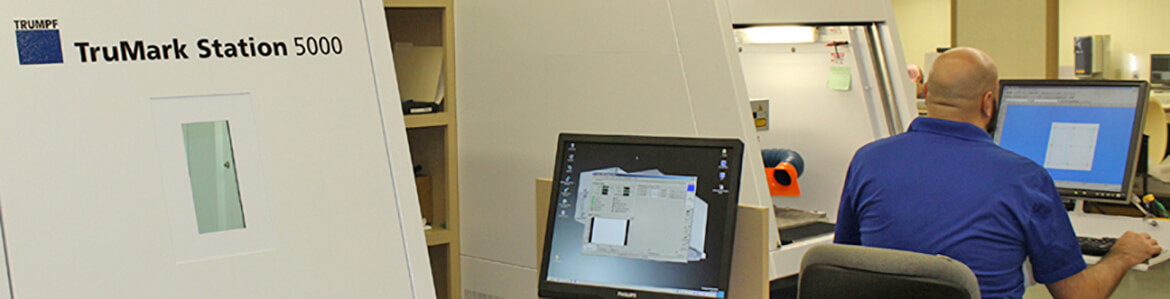
We utilize several Trumpf TruMark Laser Marking stations to laser mark parts. Laser marking utilizes a computer controlled laser beam to mark the surface while leaving the surface intact. Some of the advantages to laser marking include, a permanent long-lasting marking, high precision, design flexibility, cost effective and quick cycle times. It is important to note that not all plastics can be laser marked due to their chemical structure.
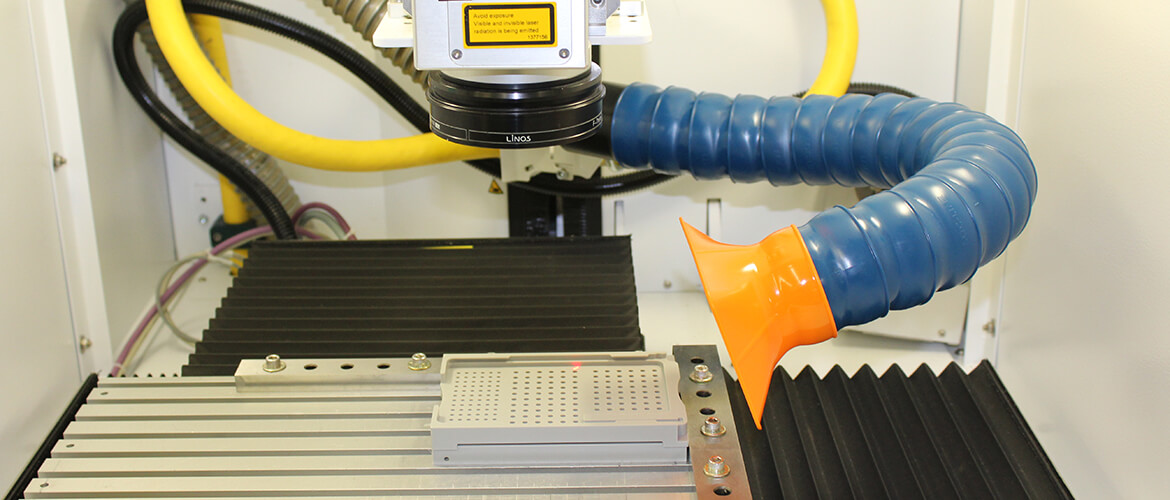
Depending on the material type and application laser marking is an ideal way to mark production parts.
Contact us to evaluate your parts for laser marking.
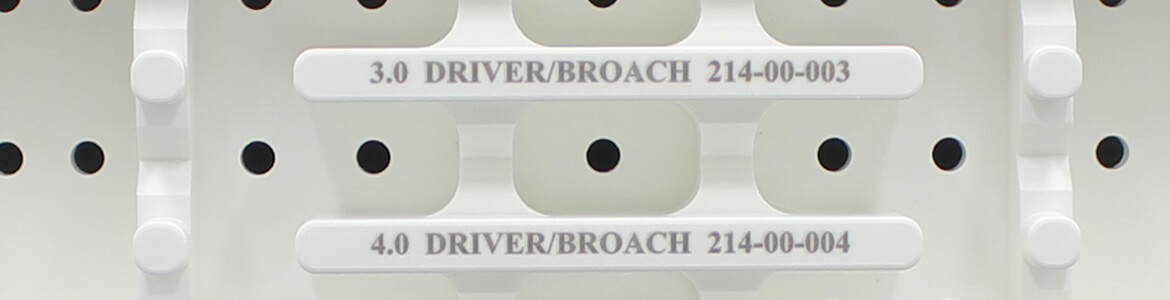
UDI Laser Marking
With the new Unique Device Identification (UDI) requirements, Boedeker Plastics, Inc. added UDI laser marking technology in 2018 for medical industry clients. Boedeker Plastics, Inc. was the first company in North America to combine ISO Certified 13485 plastics only precision CNC machining with in-house UDI laser marking technology. This added technology offers medical customers a single source solution for high quality parts that comply with the FDA’s new UDI labeling requirements.
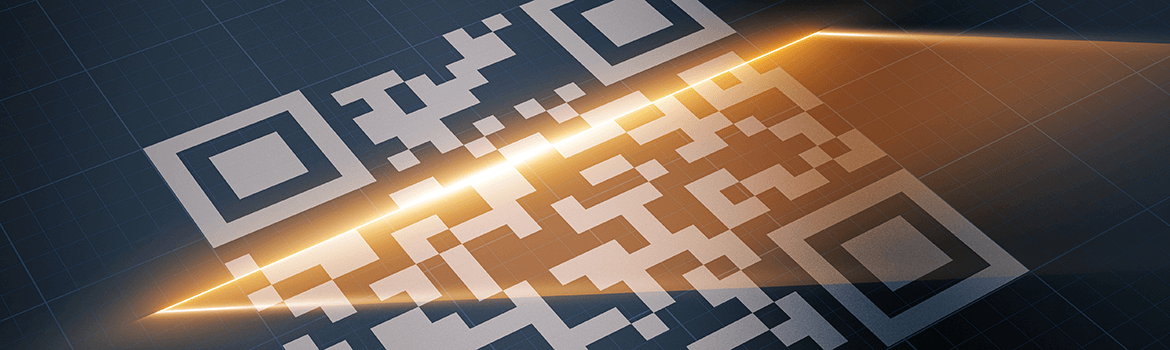
Our UDI Laser Marking system is comprised of a Worx housing and Keyence MD-X1020 Hybrid Laser Marker.
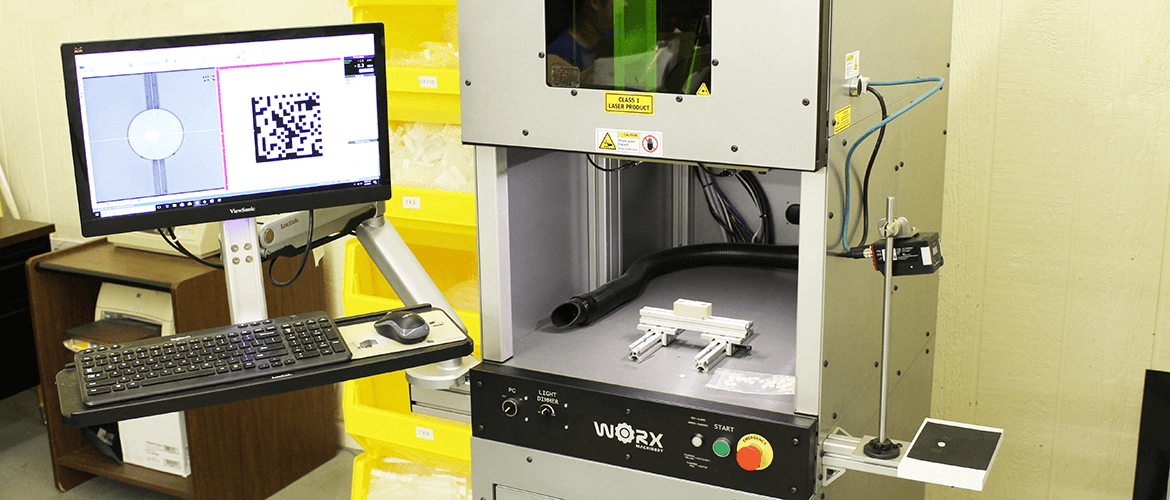
This system is equipped with a unique laser oscillation technology that combines the characteristics of both YVO4 and FIBER lasers to deliver a fine quality, high speed mark unlike any other laser system. It has a built-in camera that can also be used to measure the focal distance and automatically adjust to eliminate marking defects caused by focus misalignment.
The camera can also be used to read and verify 2D codes, which automatically marks the target (part) and then verifies the printed data for readability. In addition to pass/fail verification, the laser marker can judge the marking quality of the 2D code after it is marked and output this value giving it comprehensive traceability.
The UDI system has specialized marking software to generate 2D label codes that are programed from the customer’s label parameters. The image below shows a part after it has been laser marked using our UDI laser marking.
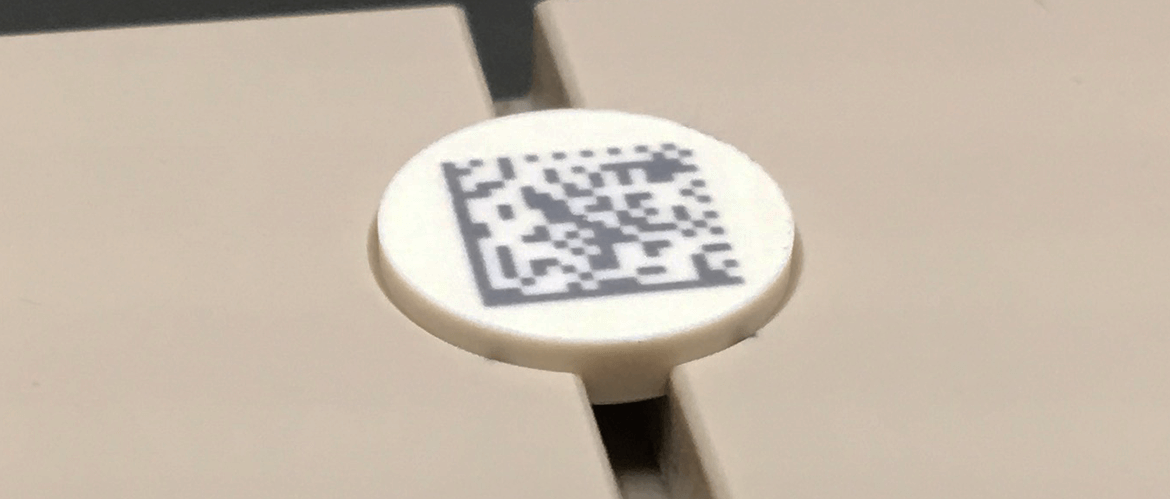
Below in Figures 1 & 2 are screen views from our marking software. The screen view is split showing the target (part) on the left and the label code on the right. The target (part) image is fed to the software from the systems camera that is focused on the target (part) during the marking process. The camera also inspects using pass/fail verification along with measuring the quality and records this value giving it comprehensive traceability.
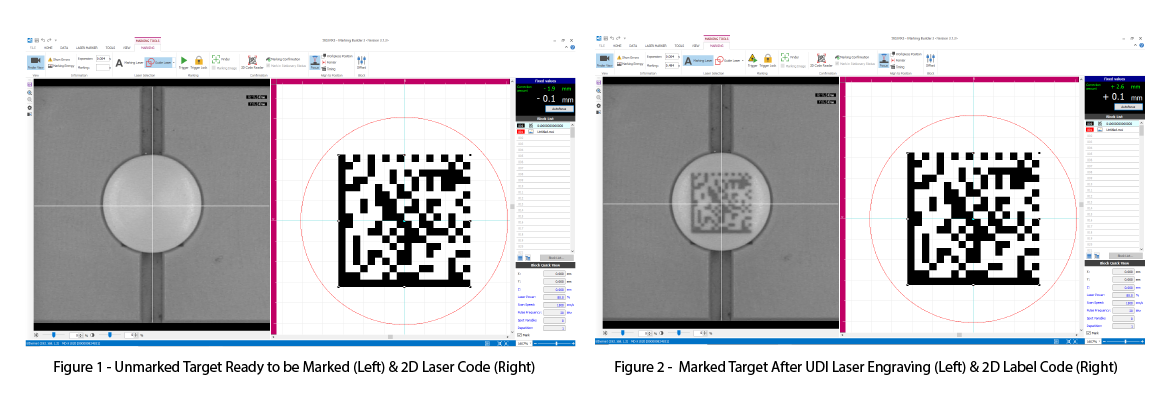
CONTACT US - For more information on Boedeker Plastics, Inc. or our UDI laser marking and medical part manufacturing capabilities and services.
For detailed information on UDI, please reference the FDA’s web page on Unique Device Identification – UDI