What is Mold Flow Analysis?
Mold Flow Analysis is a computer simulated analytical process that simulates an injection molding cycle with a specific plastic, temperature, time, pressure and other processing parameters that provides detailed mold flow data. The data is represented by a color map (as shown below) that indicates the flow characteristics of the polymer during the molding process.

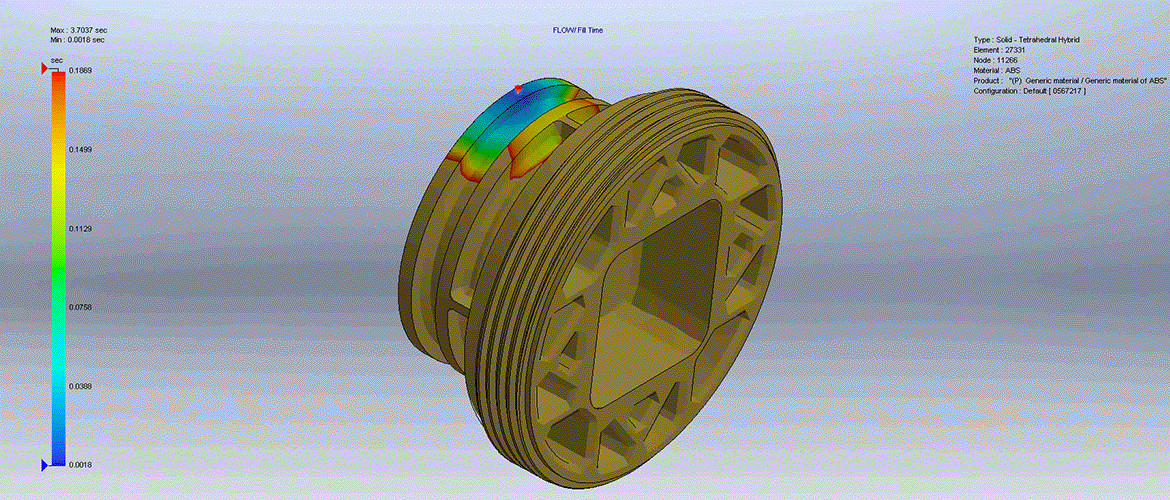
With the wide range of processing parameters that a MFA can process it can help catch potential problem areas with the part or tooling design related to the runner system, gate location, sprue, cooling lines, shear stress, fiber orientation, part cavity and many other aspects that impact a tool's performance utilizing a wide variety of simulated processing parameters.
A Mold Flow Analysis is conducted by an experienced engineer that understands plastic part design, injection mold design, mold making and other critical factors to successfully execute the MFA and utilize the data to optimize the part and mold design.
When should you use a Mold Flow Analysis?
A mold flow analysis should occur before the injection molding process ever begins and most importantly before the injection molding tool is manufactured. When a part has been identified as a candidate for injection molding it is critical to review the part for proper design.
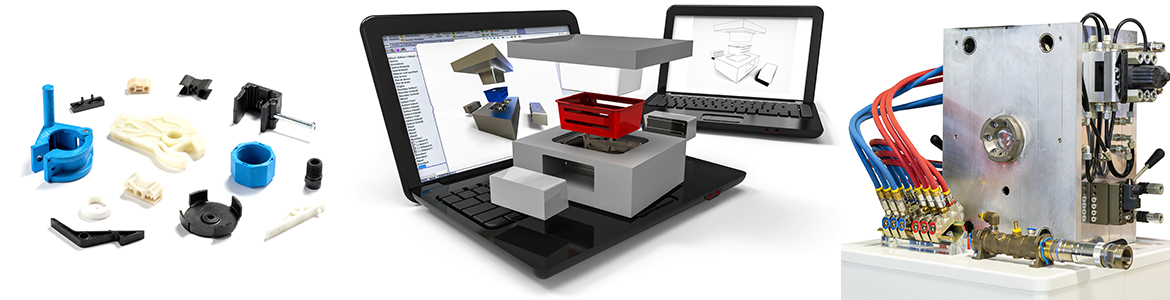
Ideally you want to work with an Injection Molding company that has Mold Flow Analysis capabilities and an experienced engineer that is an expert with injection molded plastic part design, injection mold design and mold making. By combining the MFA and an experienced engineer you can optimize your part and tool design for molding efficiency, fiber orientation, knit line location, optimal gating, ejector pin location and more.
The combination of Mold Flow Analysis and an experienced engineer can greatly reduce headaches related to tooling modifications during startup. Without MFA as part of your tooling design process it is not uncommon to experience more molding problems related to improperly designed tools, which results in excessive downtime and added tooling expenses.
Why use Boedeker Plastics, Inc. for your Mold Flow Analysis?
We are a USA owned and operated full-service plastics company that specializes in onshoring and reshoring services.
We do Injection Molding the Boedeker Way with a complete injection molding solution that includes Mold Flow Analysis services. Our MFA services are performed by our injection molding engineer who has decades of experience with injection molded plastic part design, injection mold design and mold making. MFA services are available to all Boedeker Plastics, Inc. injection molding clients as part of our complete injection molding solution and not as a standalone service.
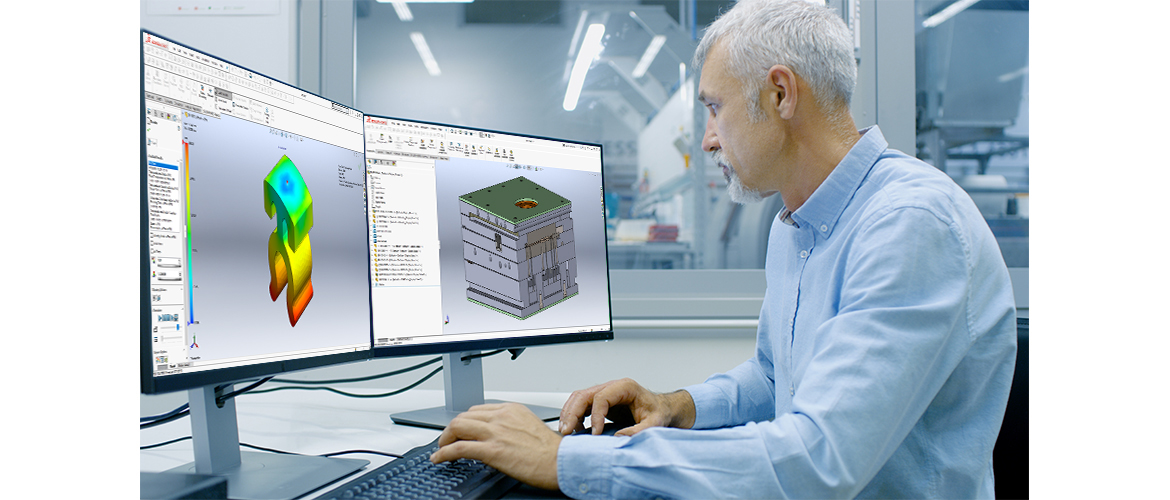
Before the MFA is performed, we evaluate the part and volume to determine if injection molding is the ideal process for production. In some cases, part volume does not warrant molding and CNC precision machining is more suitable.
After a part is identified as a suitable candidate, our Engineer performs the MFA. Our MFA process involves many parameters that impact tooling such as part geometry, thermoplastic material selection, knit lines, fiber orientation (with filled materials), gate location, gate design, ejector pin location, and many other parameters to optimize the tool design and part production.
Our Engineer and Technical Sales Team work with our clients to discuss any changes that need to be made throughout the MFA and design process to ensure that all of the clients' requirements are met to their satisfaction.
We offer a Complete Injection Molding Service and work with our clients with our in-house services which can take a concept to full scale manufacturing. In addition to MFA, our clients have access to our CNC Plastics Only Machine Shop for functional part prototyping, Unmatched Technical Support, Finite Element Analysis, Tooling Manufacturing, Injection Molding, Assembly and JIT Supply Service.
Contact Us to discuss your injection molded part requirements and have Team Boedeker evaluate your project for molding and avoid expensive tooling errors with our Mold Flow Analysis services.