Why Boedeker Near Net Shapes?
Machining is a subtractive manufacturing process, in some cases a machined part may require the removal of a large volume of material, as shown in Figure 1. Parts like this have added production costs due to the longer machine time and large volume of material that must be machined away to achieve the finished geometry.
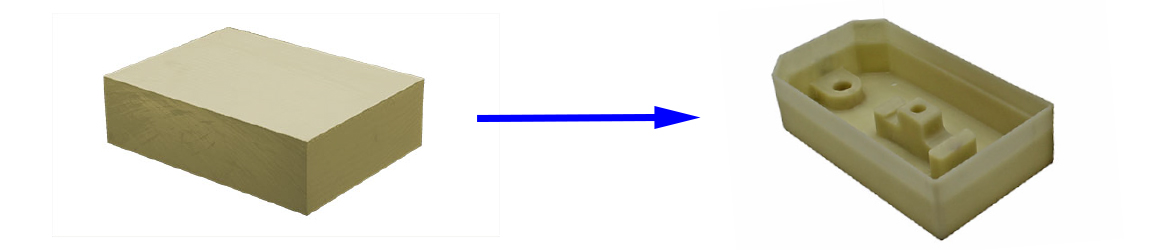
Figure 1 - Typical Plate Used to Machine Finished Part
Longer machining times are costly and removing excessive material adds additional cost to the production part cost for the manufacturer and the end customer. When machining higher performance plastics like Ultem, Radel, PPS, PEEK, Torlon PAI and others the wasted material that has to be removed can drive the finished machined part costs substantially higher.
Instead of machining a part as shown in Figure 1 from a traditional plate of material, a Boedeker near net shape can be used instead as shown below in Figure 2.
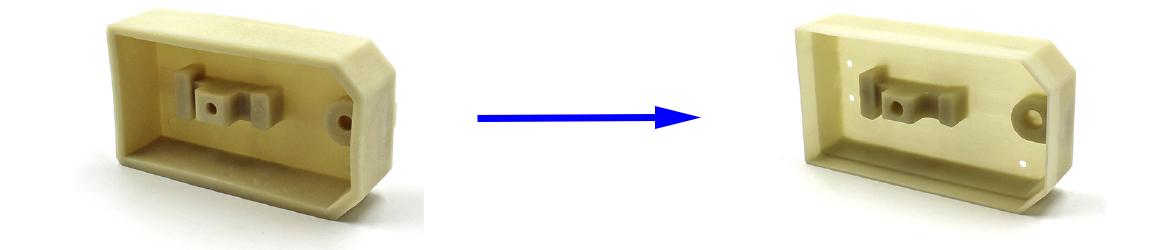
Figure 2 - Boedeker Near Net Shape to Machined Finished Part
The Boedeker Near Net Shape greatly reduces the production costs of the finished machined part by reducing machine time and eliminating the excessive wasted material for parts that require a high volume of material.
What are Boedeker Near Net Shapes (NNS)?
The near net shape is an injection molded shape with geometry that is engineered to be finish machined to the customer's final part dimensions and tolerances as shown in Figure 3. NNS technology is available with any melt processible injection molded materials, from commodity resins like HDPE, PP, Nylon, Acetal to advanced engineering resins like Ultem, PEEK, Torlon and others.
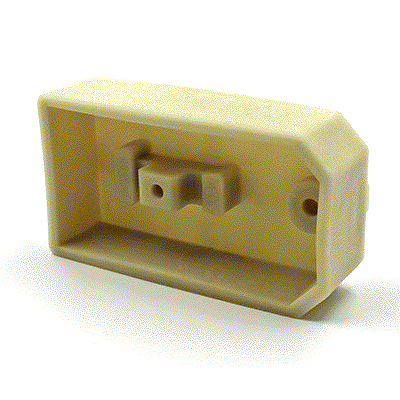
Figure 3 - Boedeker Near Net Shape & Machined Finished Part
When to use Boedeker Near Net Shapes?
Boedeker NNS Technology offers engineers a more cost-effective approach to yielding their advanced engineered polymer component over the traditional methods of simply machining from a stock shape or injection molding. To determine if NNS is right for your application, one needs to consider a few very important aspects pertaining to their application and situation. Figure 4 provides a general guideline for when NNS should be considered compared to traditional processing methods of machining from stock shapes or injection molding. Contact Us, our experts can evaluate your part and determine if it is a fit for a Boedeker NNS solution.
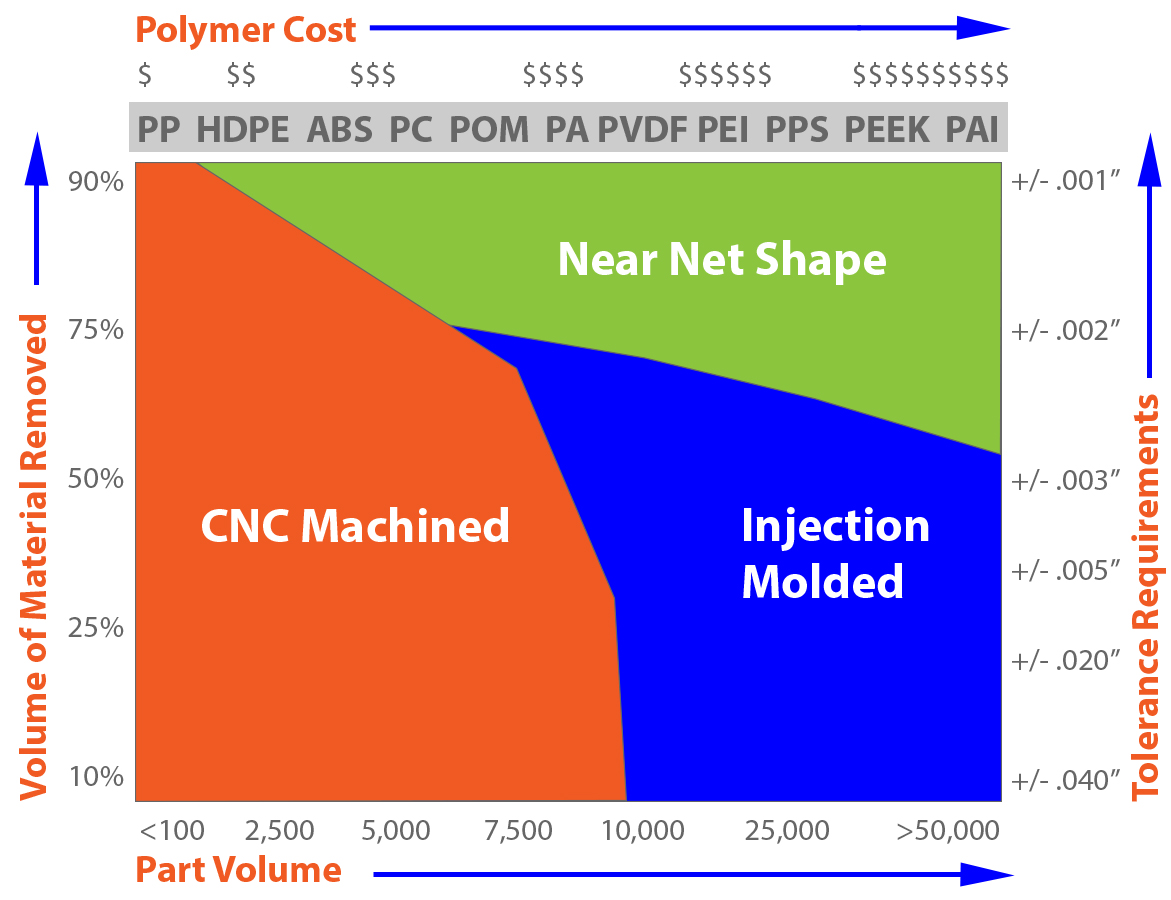
Figure 4 - NNS General Guidelines
How critical are the tolerances on your part?
Can the part be direct injection molded without any finish machining? If tolerances are so tight that molding cannot achieve the desired results, and finish machining is required, then NNS could be an option.
How much machining is required?
If a significant portion of the part volume needs to be machined away, reduction of this waste via NNS could also be a benefit resulting in significant cost savings. This will particularly be the case, the more expensive the raw material being considered is. If greater than 50% of the part volume is being removed, one should consider NNS. Ideal materials for NNS include Nylon PA, Acetal POM, PC, PSU, Ultem PEI, Radel PPSU, PPS, PEEK, and Torlon PAI.
What are the overall volume requirements for your part?
Finally, the overall part volume is important to consider, as one must purchase or amortize the initial cost of the NNS mold. As mentioned previously, NNS molding tools are much more cost effective compared to typical injection molding tooling. NNS tools are not concerned with surface finish nor exact dimensional tolerances, since the parts will be finish machined. As a result, the tooling investment is significantly lower, and this cost can be covered over a much lower volume compared to traditional injection molding tooling. The NNS approach is often used for as little as 500-piece quantities to well over several thousand pieces per year.
What are other benefits of Boedeker Near Net Shapes?
NNS technology not only reduces the cost of producing CNC machined plastic parts but gives engineers the option to specify even higher performance plastics that can offer greater life in application.
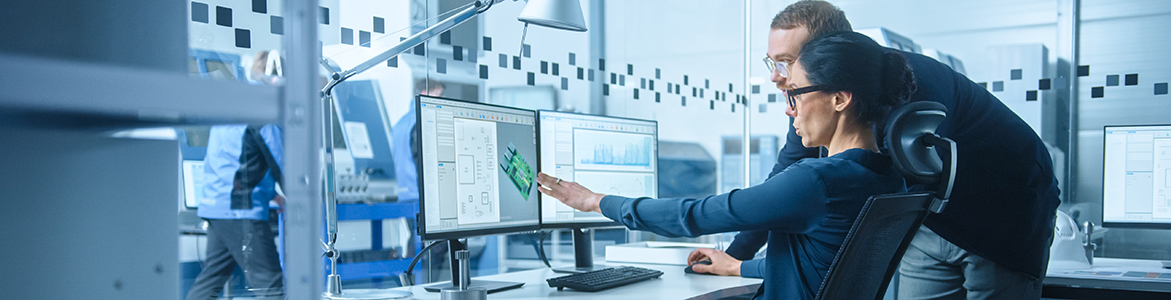
Plastics that offer improved chemical resistance, higher operating temp capabilities, and higher mechanical properties can now be specified that may have been cost prohibitive in the past with traditional CNC machining.
NNS allows for initial lower part costs and more importantly lower cost-in-use with improved performance in the application.
Common applications that can benefit from NNS include high performance plastic bearing and wear components, structural components, electrical insulating components and numerous other components across a wide range applications and industries.
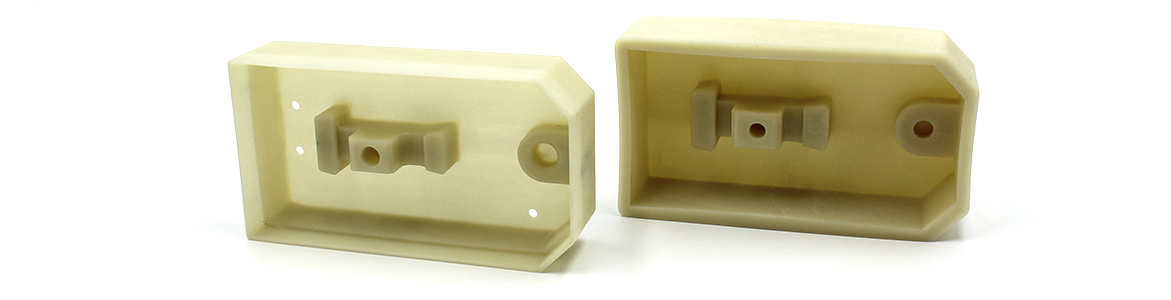
Contact Us, our experts can evaluate your part and determine if it is a fit for a Boedeker NNS solution.