Customer Notification - Plastics Global Supply Chain Experiencing Shortages and Delays
Important: If you use plastic stock shapes, machined plastic components or injection molded plastics components, your immediate attention to this notification is requested.
November 9, 2021
Customer Notification
Ref: Global Supply Chain experiencing shortages and delays
To our valued customers, the plastics raw material industry is experiencing raw material shortages beyond anything we have ever seen, logistic delays across the entire spectrum and production lead times 5-6 times longer than industry standard based on 2020 averages. Upwards of 20 weeks seems to be the normal quoted delivery for production of plastic stock shapes, some even longer.
All indications are that this will run into and through 2022 and quite possibly a portion of 2023.
What we are doing at Boedeker Plastics to protect you and your customers:
- Working closely with all plastic stock shape suppliers to provide a steady stream of product into our inventory to support you and your customers.
- Placing advance orders to cover inventory needs throughout 2022 on all products, sizes, and shapes.
- Working with customers to secure products to cover their demands for 2022, in both plastic stock shapes and finished machined or injection molded parts.
- Passing on our discounted shipping rates and surcharge fees from our carriers.
- Adding additional sawing equipment to quickly cut your products to size to avoid extreme length surcharges being instituted by the freight industry.
What you should expect for the next 12-18 months:
- The potential for shortages, delays, and due dates not being met due to raw material challenges.
- Increased prices for raw materials, even on a product that is on order and still to be produced and delivered. Our suppliers are setting the price daily and will not guarantee any price until the product is produced. This leads to the potential for your pricing needing to be increased before shipping your order. You need to be aware of this and make sure your customer understands the potential for price increases up to the product being delivered.
- Shipment delays, parcel carriers such as UPS and FedEx, along with all LTL carriers, seem to be overwhelmed, and normal deliveries seem to be taking upwards of 2-3 days longer than what is standard. Also, delivery guarantees have been suspended, so no claims for what would be considered a late delivery, are allowed.
- Freight costs are skyrocketing due to new extreme length surcharges. Customers will need to reassess the need for products with lengths up to and longer than 96 inches. Some of these longer length shipments have added extreme length fees upwards of $1,000.00 from certain carriers.
- You will see a proactive approach by our customer service and sales teams to work with your buyers to make sure the products you order from Team Boedeker avoid these extreme length surcharges. We want to offer our same day cut to size service to your buyers, to keep shipping costs in check, reduce labor and handling costs on your end, along with streamlining packaging to reduce package size/area that also plays into determining a final freight cost.
- We are also hearing of freight carriers suspending pickups and deliveries into specific areas, such as rural areas, or adding additional fees to deliver to these areas, along with delayed shipments due to accessing these areas only once or twice per week, instead of daily.
- Continued open communication from Team Boedeker on these ongoing challenges and our efforts to protect you and your customers.
What we need from you:
- Forecasts, forecasts and again, forecasts. We recommend that you look at your current and future requirements and provide us with a forecast. This will help us communicate ongoing needs to our raw material suppliers and secure product to meet demand into 2022.
- Plan for longer lead times, update your BOMs to include raw material deliveries extending to 20 plus weeks. This planning will help you get us orders in time to meet your demand.
- Increase your internal stock levels of finished components, to protect against production delays.
- Review your ordering practices to make sure raw material sizes are ordered to a size that does not fall into an extreme length category to avoid the pricey surcharges from freight companies.
- Consolidate shipments to control freight costs.
- Review current material callouts and determine if substitutions are acceptable due to long lead times and resin shortages.
- Work closely with your Team Boedeker representative to protect you, your company, and your customer. We are here to assist you with all these challenges.
Your quick attention to this notification will help us help you solidify a steady supply of product and minimize disruptions of supply.
We are here to assist, please do not hesitate to contact one of our team members for more information on this subject or to setup a meeting to discuss the products you use or plan to use over the next 12-18 months.
Sincerely,
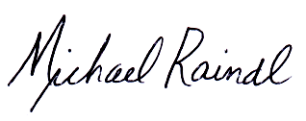
Michael Raindl
General Manager
Boedeker Plastics, Inc.
2681